How Permadec Made GRP Formwork History at Majors Road Bridge
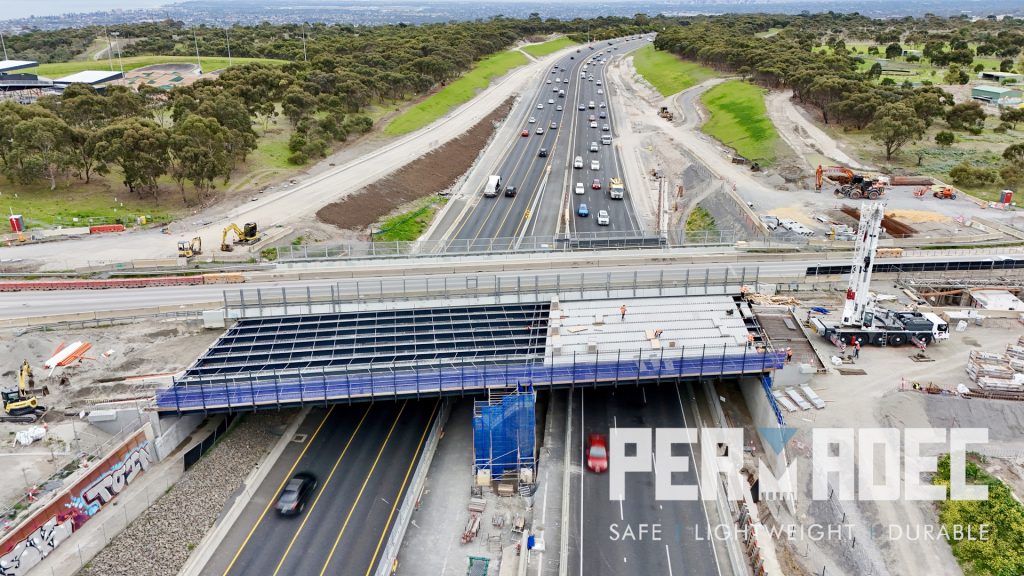
Permadec recently played a key role in the Majors Road Interchange upgrade in South Australia, delivering the state’s first-ever installation of GRP permanent formwork. As part of a bridge widening project led by Acciona, with Wallbridge Gilbert Aztec (WGA) as consulting engineers and the Department for Infrastructure and Transport (DIT) South Australia as the client.
Notably, Permadec supplied a combination of standard, custom, and innovative cantilever GRP panels. Premier Constructions Australia installed Permadec panels.
This successful installation not only marks a significant step forward in bridge formwork innovation, but also highlights the value of early coordination with WGA. By working closely during the design phase, Permadec was able to tailor rib spacings to avoid clashes with shear studs. This ensured seamless installation and reducing the risk of on-site modifications.
Learn more about the Majors Road Interchange Project on the DIT website, or view our Permadec project case study here.
Why GRP Formwork is Ideal for Bridge Construction
The Majors Road Interchange project is a prime example of how Glass Reinforced Polymer (GRP) permanent formwork is reshaping the way bridges are built in Australia. With demanding site conditions and a need for durability, GRP offered a number of distinct advantages over traditional materials.
Lightweight and Easy to Handle
GRP panels are significantly lighter than concrete alternatives, making them easier to transport and install. This is especially beneficial in complex bridge environments with limited access or safety restrictions.
Corrosion Resistant
GRP has a far greater resistance to corrosion. This makes it particularly well-suited to exposed infrastructure such as bridges, which are subject to weather extremes, road runoff, and coastal conditions. Over time, this reduces maintenance needs and extends the lifespan of the structure.
Permanent and Reduced Maintenance
As a permanent formwork solution, GRP panels remain in place after the concrete pour, eliminating the need for removal and reducing on-site labour. This not only speeds up construction, but also enhances worker safety by reducing time spent at height or over open spans.
Precision-Manufactured to Suit Complex Designs
Permadec’s GRP panels can be custom-fabricated to suit a wide range of bridge geometries — including varying deck depths, curved edges, and cantilevers. At Majors Road, we delivered bespoke panel configurations to integrate seamlessly between the new and existing bridge structures.
Efficient Edge Treatment with Cantilever Panels
One of the key innovations on this project was the use of GRP cantilever panels. As a result, these reduced the need for conventional edge formwork, streamlining construction and minimising on-site labour. This not only simplified the build process, but also created a cleaner and more consistent finish.
This innovative formwork solution provided a lightweight, durable, and efficient alternative to traditional methods, helping us deliver high-quality outcomes.
Project Engineer, Premier Constructions Australia
Collaborative Design to Prevent On-Site Issues
At the heart of the Majors Road success was early and detailed coordination with Wallbridge Gilbert Aztec (WGA). Permadec worked closely with the engineering team to ensure the GRP panels aligned precisely with structural elements. In particular, ensuring rib spacings were matched to shear stud positions. This level of upfront design integration avoided on-site clashes. It also reduced the need for reactive adjustments during installation.
The result was a seamless interface between the GRP formwork and reinforcement layout. This allowed Premier Constructions to proceed efficiently with minimal interruption to the programme.